Rio Tinto and Hydro Invest $45 Million to Cut Aluminum Emissions
Aluminum is everywhere, from cars to cans, but its production is a major carbon polluter. With global aluminum demand soaring, Rio Tinto and Hydro will $45 million in carbon capture tech to cut emissions. Could this be the breakthrough the industry needs?
The Carbon Footprint of Aluminum: A Heavyweight Problem
Aluminum production accounts for about 2% of global carbon emissions. The industry emits about 1.1 billion metric tons of CO₂ per year. That’s the same as the emissions from 150 million U.S. homes.
The electrolysis process alone is responsible for 791 million metric tons. Electrolysis is the main step in aluminum smelting. It uses carbon anodes, which release CO₂ during the process. This stage accounts for around 75% of a smelter’s direct CO₂ emissions.
With transportation, construction, and packaging relying on aluminum, we must reduce its environmental impact. Many aluminum producers are now seeking ways to cut emissions and reach net-zero targets.
A $45 Million Push for Carbon Capture
To tackle this, Rio Tinto and Hydro will invest $45 million over the next five years to develop carbon capture technologies for aluminum smelting. Smelting takes up most of the total GHG emissions of aluminum production.
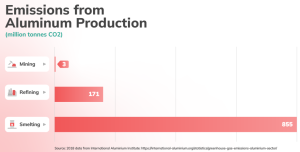
The partnership focuses on finding, testing, and scaling up methods to capture and store CO₂ emissions from the electrolysis process. The initiative includes:
- Testing carbon capture technologies from laboratory research to real-world applications.
- Running pilot projects at Rio Tinto’s facilities in Europe and Hydro’s sites in Norway.
- Sharing research, costs, and expertise to accelerate progress.
Why Carbon Capture Is Difficult in Aluminum Smelting
Capturing carbon in aluminum production is more challenging than in other industries like power generation. This is because CO₂ levels in aluminum smelter emissions are extremely low (only about 1% by volume). This makes conventional carbon capture methods less effective.
There are two main approaches to capturing CO₂ from aluminum smelters:
- Point source carbon capture: This technology captures emissions at the source but must be adapted for lower CO₂ concentrations.
- Direct air capture (DAC): While typically used to remove CO₂ from the atmosphere, DAC could be modified to work in aluminum smelters.
Both methods need significant development to move from the lab to full-scale commercial use. This is where Rio Tinto and Hydro’s investment plays a key role in advancing these technologies.
Racing Toward Net-Zero: Can They Pull It Off?
This partnership is part of a broader push toward decarbonizing aluminum production. Both companies have already been working on independent initiatives, including:
- ELYSIS (Rio Tinto & Alcoa): A joint venture focused on developing carbon-free aluminum smelting technology.
- HalZero (Hydro): A new smelting process that eliminates CO₂ emissions from aluminum production.
While these long-term projects aim to create zero-emission aluminum, carbon capture can help reduce emissions from existing smelters. By combining their expertise, Rio Tinto and Hydro hope to make these technologies commercially viable sooner.
The Surge in Demand for Green Aluminum
As industries transition toward sustainable materials, demand for low-carbon aluminum is rising. Companies in automotive, construction, and packaging are seeking greener alternatives to meet climate targets.
Global aluminum demand is projected to rise nearly 40% by 2030, according to CRU International’s report for the International Aluminium Institute (IAI). The industry must produce an extra 33.3 million metric tons (Mt), increasing from 86.2 Mt in 2020 to 119.5 Mt in 2030. Key drivers of this growth include transportation, construction, packaging, and the electrical sector, which will account for 75% of total demand.
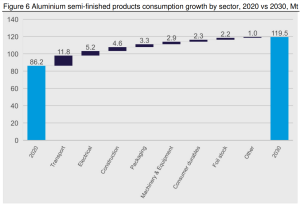
China will remain the largest consumer of semi-finished aluminum products by 2030. The Asian country makes up for over 45% of the market since 2015.
As industries push for lighter, more sustainable materials, aluminum’s role in global manufacturing will expand. This emphasizes the need for efficient production and decarbonization efforts to meet the rising demand sustainably.
Regulations are also pushing aluminum producers to reduce emissions. Governments worldwide are setting stricter carbon limits and introducing carbon pricing mechanisms that penalize high-emission industries. Carbon capture for aluminum production could give Rio Tinto and Hydro a competitive edge in this evolving market.
Beyond Carbon Capture: Other Ways to Cut Emissions
Beyond carbon capture, the aluminum industry is exploring other solutions to reduce emissions and energy use:
- Recycled Aluminum: Producing aluminum from recycled materials uses 95% less energy than primary production. Expanding aluminum recycling can significantly cut industry-wide emissions.
- Inert Anodes: Traditional carbon anodes release CO₂ during electrolysis, but inert anodes could eliminate these emissions. This technology is still in development but shows great potential.
- Renewable Energy-Powered Smelters: Switching from fossil fuels to solar, wind, or hydroelectric power can drastically reduce emissions from aluminum production.
By combining these strategies with carbon capture, the industry can move closer to achieving net-zero emissions.
Rio Tinto and Hydro’s partnership marks a major step toward decarbonizing aluminum smelting. If successful, their investment could lead to groundbreaking advancements that benefit the entire sector. By working together, they are taking a critical step toward making low-carbon aluminum a reality—a move that aligns with global climate goals and industry sustainability efforts.
- READ MORE: Rio Tinto and Imperial College London Launch $150 Million Partnership to Power the Energy Transition
The post Rio Tinto and Hydro Invest $45 Million to Cut Aluminum Emissions appeared first on Carbon Credits.